Understanding and Complying with Lifting Regulations in the Home & Garden Industry
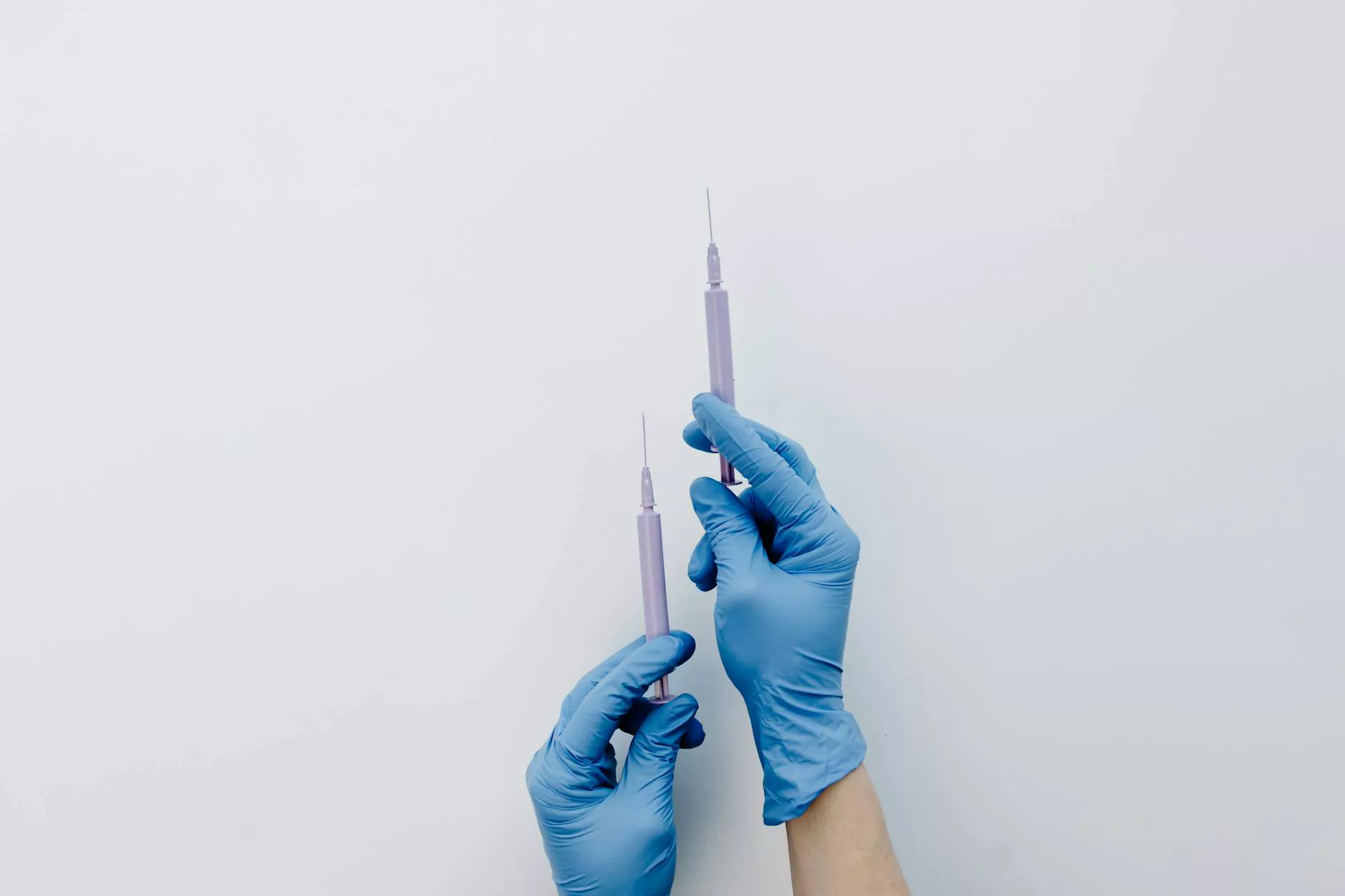
The Home & Garden industry encompasses a diverse range of services and products, from landscaping and gardening to pest control and outdoor maintenance. While this sector offers numerous opportunities for growth and innovation, it also carries significant responsibilities regarding health and safety standards, especially in relation to lifting operations. Proper adherence to lifting regulations is vital to ensure worker safety, prevent accidents, and maintain high-quality service delivery.
What Are Lifting Regulations and Why Are They Crucial in the Home & Garden Sector?
Lifting regulations are legislative frameworks and best practices designed to safeguard workers from the hazards associated with lifting heavy objects, equipment, and materials. These regulations are essential across various industries, including the Home & Garden sector, where manual handling of plants, gardening machinery, and heavy garden fixtures is common.
Ensuring compliance with these regulations helps mitigate risks such as musculoskeletal injuries, falls, and accidents involving mechanical handling devices. Moreover, adherence to lifting regulations demonstrates a company’s commitment to safety, enhances its reputation, and reduces potential legal liabilities.
The Legal Framework Governing Lifting Operations in the UK
The primary legislation in the UK that governs lifting operations and manual handling is the Manual Handling Operations Regulations 1992 (as amended). These regulations impose duties on employers and workers to minimize risks associated with manual handling tasks.
Additionally, the Provision and Use of Work Equipment Regulations 1998 (PUWER) oversee the safety of lifting equipment such as cranes, hoists, and forklifts. The Lifting Operations and Lifting Equipment Regulations 1998 (LOLER) focus specifically on the planning, installation, and inspection of lifting equipment used in work activities.
It's mandatory for businesses in the Home & Garden industry to understand and comply with these regulations to promote a safe working environment.
Key Components of Effective Lifting Regulation Compliance
- Risk Assessment: Conduct thorough evaluations of lifting tasks to identify potential hazards and implement control measures.
- Proper Training: Ensure all employees involved in lifting operations receive adequate training on safe lifting techniques and equipment use.
- Equipment Safety Checks: Regular inspections and maintenance of lifting machinery and accessories.
- Use of Appropriate Equipment: Select suitable lifting devices for the task, such as cranes, lifts, or manual handling aids.
- Supervision and Monitoring: Continuous oversight to guarantee adherence to safety procedures.
- Documentation and Record-Keeping: Maintain records of risk assessments, training sessions, inspections, and incident reports.
The Role of SafePlant UK in Ensuring Compliance with Lifting Regulations
At SafePlant UK, we specialize in providing comprehensive solutions that uphold lifting regulations across the Home & Garden sector, including services for Gardeners and Pest Control professionals. Our expertise in safety management ensures that every lifting operation is performed securely, efficiently, and in compliance with all legal standards.
Consultation and Risk Assessment
We begin by conducting detailed site assessments and risk evaluations, tailored specifically to the unique requirements of garden-related tasks and pest control operations. Our experts identify potential hazards associated with lifting loads such as heavy plant pots, machinery, fencing panels, or equipment used in pest management.
Training and Certification Programs
SafePlant UK provides specialized training programs designed to educate workers on safe lifting practices, proper manual handling techniques, and the correct use of lifting equipment. Our training is compliant with the latest lifting regulations and ensures your team can operate confidently and safely.
Equipment Supply and Maintenance
We offer a range of professionally maintained lifting equipment, including harnesses, cranes, lifts, and manual handling aids suitable for the Home & Garden environment. Our maintenance protocols align with LOLER and PUWER standards, guaranteeing equipment safety and reliability.
Ongoing Support and Compliance Management
Our team provides continuous support, including periodic inspections, accident prevention strategies, and updates on legislative changes related to lifting regulations. This proactive approach helps your business maintain compliance and safeguard your workforce.
Best Practices for Safe Lifting in the Home & Garden Sector
Implementing best practices is essential to prevent injuries and legal issues. Here are crucial tips for safe lifting:
- Plan the Lift: Determine the weight, size, and nature of the load. Decide whether mechanical assistance is necessary.
- Use Proper Techniques: Lift with your legs, keep the load close to your body, and avoid twisting or sudden movements.
- Utilize Appropriate Equipment: Use lifting aids when dealing with heavy or awkward loads.
- Maintain a Clear Path: Ensure the route is free from obstructions before lifting or moving loads.
- Never Overreach: Keep loads within your comfortable reach and avoid excessive stretching.
Impact of Non-Compliance with Lifting Regulations
Failure to adhere to lifting regulations can lead to severe consequences, including:
- Injuries and Fatalities: Musculoskeletal injuries, fractures, or even fatal accidents resulting from improper lifting practices.
- Legal Penalties: Fines, sanctions, or prosecution under health and safety laws.
- Financial Losses: Compensation claims, increased insurance premiums, and operational downtime.
- Reputation Damage: Loss of customer trust and credibility within the industry.
Future Trends and Innovations in Lifting Safety for the Home & Garden Industry
The Home & Garden sector is evolving with technological advancements that enhance lifting safety and operational efficiency. These include:
- Automation and Robotics: Use of automated lifts and robotic assistive devices to handle heavy or hazardous loads.
- Smart Monitoring Systems: Sensors and IoT-enabled equipment that monitor load weight, stability, and equipment condition in real-time.
- Enhanced Training Modules: Virtual reality and e-learning platforms to improve training effectiveness.
- Eco-Friendly Equipment: Adoption of energy-efficient and sustainable lifting solutions aligned with environmental standards.
Conclusion: Prioritizing Safety and Compliance in All Lifting Operations
In the dynamic world of Home & Garden services, mastering lifting regulations is not just a legal requirement but a fundamental aspect of ethical business practices. It fosters a safety-first culture, protects workers, and sustains operational excellence. Companies like SafePlant UK are dedicated to supporting your business through expert consultancy, state-of-the-art equipment, and comprehensive training programs tailored to your specific needs.
By prioritizing lifting safety and maintaining strict compliance with lifting regulations, your business can thrive in a competitive environment, confidently expanding your services while safeguarding your team and clients.
Invest in safety today to build a resilient, compliant, and reputable Home & Garden enterprise. Remember, safety is an ongoing journey that requires vigilance, education, and the right resources—partner with professionals like SafePlant UK to lead the way.